Innovation, Manufacturing, and Choosing Caster wheel manufacturer for Unmatched Performance
In the intricate ballet of global industry and daily life, movement is fundamental. From the colossal machinery shaping skyscrapers to the hospital bed ensuring patient comfort, and the humble office chair facilitating productivity, one component silently bears the weight of progress: the caster wheel. More than just simple wheels, casters are sophisticated engineering solutions designed for load-bearing, maneuverability, durability, and safety across countless applications.
This comprehensive guide delves deep into the world of caster wheels. We’ll explore their types, applications, critical manufacturing processes, and the factors defining true quality. Central to this exploration is Goodich, a leading caster wheel manufacturer renowned for innovation, reliability, and global reach under the banner of Guangdong Goodich Hardware Co., Ltd., a premier Chinese caster wheel manufacturer. Whether you’re an industrial procurement specialist, a facilities manager, or simply value robust engineering, understanding caster wheels is key to optimizing mobility and efficiency.
Understanding Caster Wheels – Beyond the Basics
- Anatomy of a Caster:
- Wheel: The rolling element, available in diverse materials (Polyurethane, Nylon, Phenolic, Rubber, Thermoplastic Rubber (TPR), Cast Iron, Steel, Vulkollan®) and tread designs. Determines load capacity, floor friendliness, noise level, and resistance to environment/terrain.
- Mounting: The interface attaching the caster to the equipment. Common types include:
- Top Plate: Fixed bolt pattern (e.g., 3″x3″, 4″x4″, 4.5″x6.25″).
- Threaded Stem: Male or female threads screw into a receiving socket.
- Grip Ring Stem: Presses into a slightly undersized hole, held by friction.
- Hollow Kingpin: Allows bolting directly through the kingpin.
- Fork (Yoke): The U-shaped component holding the wheel axle. Material (stamped steel, forged steel, ductile iron) and design impact strength and swivel performance.
- Swivel Mechanism: Allows the caster to rotate 360 degrees. Critical components:
- Kingpin: The central pivot bolt/axle. Can be fixed or thrust-bearing assisted.
- Raceway: The smooth surface the ball bearings roll on. Precision machining is vital.
- Bearings: Reduce friction for smooth swiveling. Types include plain bore (no bearings), ball bearings, roller bearings, precision ball bearings. Sealed bearings protect against contaminants.
- Brakes (Optional): Mechanisms to lock movement:
- Wheel Lock: Prevents the wheel from rotating.
- Swivel Lock/Total Lock: Prevents both wheel rotation and swiveling.
- Position Lock: Locks the swivel in a specific direction while allowing wheel roll.
- Floor Lock: Uses a pad to grip the floor surface.
- Fundamental Caster Types:
- Rigid (Fixed) Casters: Wheel does not swivel. Provides straight-line tracking, essential for stability under heavy loads or long equipment. Requires two or more swivel casters on the same piece of equipment for maneuverability.
- Swivel Casters: Wheel rotates 360 degrees around the kingpin. Provides maximum maneuverability, essential for navigating tight spaces. Requires careful selection and potentially brakes for control under heavy loads.
- Dual Wheel Casters: Feature two wheels side-by-side within a single fork. Offer greater stability, higher load capacity (distributed over two wheels), and better performance over uneven surfaces or small debris compared to a single wheel of similar total capacity.
- Kingpinless Casters: Eliminate the traditional kingpin bolt. Use a precision thrust bearing assembly integrated into the top of the yoke. Benefits include lower overall height, elimination of kingpin shear risk, smoother swivel under heavy loads, and easier maintenance. Often preferred for heavy industrial applications.
- Leveling Casters: Combine a caster wheel with a leveling foot. Allow equipment to be leveled on uneven floors while maintaining mobility when needed. Crucial for precision machinery, lab equipment, and workstations.
- Core Caster Wheel Materials & Their Applications: MaterialKey Properties Best Applications Limitations Polyurethane Excellent load capacity, wear resistance, floor protection (non-marking), good rollability, oil/grease resistant. Wide hardness range (soft to super elastic).Industrial carts, platform trucks, material handling, assembly lines, hospital equipment, food processing, clean rooms. Can be cut by sharp debris; very hard formulations can transmit vibration. Nylon High load capacity, heat resistance, chemical resistance, low moisture absorption. Very hard and durable. High-temperature environments (ovens, foundries), chemical plants, washdown areas, heavy industrial loads. Noisy, transmits vibration/shock, poor traction on wet/slippery floors, can chip on impact. Phenolic Extreme hardness, high load capacity (especially static), heat resistance, chemical resistance. Non-porous. Foundries, steel mills, high-heat applications, extremely heavy static loads (presses, machinery), chemical exposure.Very hard – noisy, transmits vibration/shock, poor traction, unsuitable for delicate floors. Rubber (Solid)Good shock absorption, quiet operation, floor protection, moderate traction. Various hardnesses. Office furniture, light industrial carts, medical equipment (quieter), indoor general use. Lower load capacity than PU/Nylon/Phenolic, can mark floors if low quality, susceptible to oils/solvents. Thermoplastic Rubber (TPR)Combines properties of rubber and plastic. Good resilience, floor protection, moderate load, quiet, cost-effective. Light-medium duty carts, service carts, institutional furniture, indoor/light outdoor use. Lower load/heat/chemical resistance than PU/Nylon/Phenolic. Can deform under heavy static loads. Cast Iron Extremely high load capacity, heat resistance, durable. Often used with rubber treads. Heavy machinery bases, industrial presses, forge equipment, railroad applications. Very heavy, noisy, damages floors, prone to rust (unless coated).Vulkollan® (Polyurethane)Premium polyurethane offering superior cut/tear resistance, exceptional load capacity & wear life, high elasticity. Extremely demanding applications: heavy-duty logistics, ports, mining, recycling, high-abuse environments. Higher cost than standard PU. Flat-Free (Semi-Pneumatic)Microcellular polyurethane foam core. No flats, good cushioning, moderate load. Outdoor equipment, garden carts, light industrial where pneumatic puncture is a risk.Lower load capacity than solid PU wheels; can develop flat spots if overloaded statically for long periods.
- Bearing Types & Impact on Performance:
- Plain Bore: Wheel rotates directly on the axle. Simplest, lowest cost. Suitable only for very light loads and low speeds. High friction, requires frequent lubrication.
- Ball Bearings: Small balls reduce friction between axle and wheel hub. Handle higher loads and speeds than plain bore. Good for general industrial use. Require sealing to prevent contamination.
- Roller Bearings: Cylindrical rollers provide a larger contact surface. Superior for very heavy radial loads. Common in heavy industrial and kingpinless casters.
- Precision (Sealed) Ball Bearings: High-quality ball bearings with integrated seals to keep lubricant in and dirt/water out. Offer the smoothest roll, longest life, and minimal maintenance under demanding conditions. Essential for medical, cleanroom, food-grade, and high-cycle applications.
The Critical Role of Caster Grease and Lubrication
Often overlooked but absolutely vital, proper lubrication is the lifeblood of high-performing, long-lasting casters, especially swivel mechanisms.
- Why Caster Grease Matters:
- Reduces Friction: Minimizes wear on the kingpin, raceway, and bearings.
- Prevents Corrosion: Forms a protective barrier against moisture and corrosive agents.
- Protects Against Contaminants: Seals out dirt, dust, grit, and other abrasives that cause premature wear.
- Ensures Smooth Swiveling: Preents the caster from “freezing up” or becoming stiff, ensuring effortless maneuverability.
- Extends Service Life: Significantly reduces wear and tear, leading to fewer replacements and lower total cost of ownership.
- Choosing the Right Caster Grease:
- High-Viscosity: Essential for staying in place and providing a durable lubricating film. Light oils wash away quickly.
- Lithium or Calcium Sulfonate Complex Base: Offer excellent water resistance, adhesion, and load-carrying capabilities.
- Extreme Pressure (EP) Additives: Crucial for heavy-load applications to prevent metal-to-metal contact under stress.
- Corrosion Inhibitors: Non-negotiable for longevity, especially in humid or washdown environments.
- Temperature Range: Must be suitable for the operating environment (e.g., high-temp grease for ovens/foundries, low-temp grease for cold storage).
- Compatibility: Should be compatible with the bearing seals (if present) and not degrade them. Silicone-based greases are often used with certain seals but may have lower load capacity.
- Proper Lubrication Practices:
- Follow Manufacturer Guidelines: Goodich provides specific lubrication recommendations for each caster series.
- Regular Inspection: Check grease levels and condition periodically (e.g., monthly in harsh environments, quarterly in standard use).
- Clean Before Re-Lubricating: Wipe away old grease and contaminants from the raceway and kingpin area before applying new grease.
- Avoid Over-Greasing: Excess grease can attract dirt and cause its own problems. Apply enough to form a protective film without excessive buildup.
- Focus on the Swivel Mechanism: While wheel bearings (if not sealed) also need lubrication, the swivel is often the most critical point.
Industrial Applications & Selecting the Right Caster
- Heavy-Duty Industrial Casters: The Backbone of Manufacturing & Logistics
- Requirements: Exceptional load capacity (often 1,000 lbs per caster or more), durability against impact and shock, resistance to chemicals/oils/grease, reliable swivel or rigid performance, robust brakes. Kingpinless designs are prevalent.
- Materials: Heavy-gauge forged steel or ductile iron forks. Wheels: High-load Polyurethane (often Vulkollan®), Nylon, Phenolic, or Cast Iron (sometimes with poly tread). Precision roller bearings.
- Goodich Solutions: Specializes in engineered casters for extreme loads found in automotive plants, steel mills, heavy machinery transport, port logistics, and mining equipment. Focus on kingpinless technology for superior reliability.
- Medical & Healthcare Casters: Safety, Silence, and Sanitation
- Requirements: Ultra-quiet operation (patient comfort), easy cleaning/disinfection (non-porous materials), excellent maneuverability with minimal effort (ergonomics), reliable brakes for patient safety (often total lock), non-marking floors, ESD options.
- Materials: Stainless steel or zinc-plated steel forks with smooth surfaces. Wheels: Soft-tread Polyurethane or specialized rubber compounds. Precision sealed ball bearings. Non-linting lubricants.
- Goodich Solutions: Offers ranges compliant with healthcare standards, featuring quiet-roll technology, antimicrobial options, and easy-clean designs for hospital beds, crash carts, IV poles, and diagnostic equipment.
- Food Processing & Washdown Environments: Hygiene is Paramount
- Requirements: Extreme corrosion resistance (stainless steel), ability to withstand high-pressure/high-temperature washdowns and caustic cleaners, non-absorbent/non-porous materials, FDA-compliant lubricants, often ESD requirements.
- Materials: 304 or 316 Stainless Steel throughout (forks, wheels, fasteners). Wheels: Solid Polyurethane (white often preferred), sometimes specific TPRs or Phenolic. Sealed precision bearings.
- Goodich Solutions: Provides full stainless steel caster systems designed to meet stringent food safety (HACCP, FDA, USDA) and pharmaceutical (GMP) requirements, ensuring hygiene and longevity in demanding washdown conditions.
- Aerospace & Automotive: Precision and Reliability
- Requirements: High precision, reliability under demanding conditions, ESD protection (sensitive components), chemical resistance (hydraulic fluids, fuels), specific load/height requirements, often specialized mounting.
- Materials: Steel or stainless steel. Wheels: ESD-safe Polyurethane, specialized compounds. High-quality bearings. Ergonomic designs for assembly lines.
- Goodich Solutions: Collaborates with aerospace and automotive OEMs to develop custom casters for assembly jigs, engine stands, component carts, and maintenance equipment, focusing on precision movement and ESD safety.
- Retail, Hospitality & Office: Aesthetics and Function
- Requirements: Good maneuverability, quiet operation, floor protection (non-marking, non-scuffing), aesthetic appeal (colors, finishes), moderate load capacity, reliable brakes for displays.
- Materials: Zinc-plated or painted steel, sometimes aluminum. Wheels: Soft Polyurethane, TPR, Rubber, or quiet-rolling nylon. Ball bearings.
- Goodich Solutions: Offers a wide range of aesthetically pleasing, high-performing casters for shelving, display units, furniture, service carts, and office chairs, balancing function with visual appeal.
The Manufacturing Edge – Inside Guangdong Goodich Hardware Co., Ltd.
As a leading Chinese caster wheel manufacturer, Guangdong Goodich Hardware Co., Ltd. leverages advanced technology, rigorous processes, and deep engineering expertise to deliver world-class caster solutions under the Goodich brand. Here’s what sets them apart:
- State-of-the-Art Facilities:
- Precision Machining: CNC machining centers ensure consistent, high-tolerance components for forks, top plates, and kingpinless assemblies.
- Advanced Molding: Injection molding for precise, high-quality polyurethane, nylon, TPR, and rubber wheels with consistent density and performance.
- Robust Forging & Stamping: For heavy-duty forged steel yokes and stamped components requiring maximum strength.
- Automated Welding: Ensures strong, consistent welds critical for load-bearing integrity.
- Sophisticated Finishing: Electroplating (zinc, chrome), painting (powder coating, wet paint), and passivation (stainless steel) for superior corrosion resistance and aesthetics.
- Automated Assembly Lines: Combine efficiency with quality control at every stage.
- Materials Science Expertise:
- Polyurethane Formulation: Goodich invests heavily in developing proprietary PU formulations for specific needs: super elasticity (Vulkollan®-like performance), extreme cut/tear resistance, ESD properties, FDA compliance, color stability, and optimized hardness.
- Metal Alloy Selection: Careful selection of steel grades (mild steel, high-tensile steel), ductile iron, and stainless steel (304, 316) based on application demands for strength, weight, and corrosion resistance.
- Bearing & Component Sourcing: Strategic partnerships with leading bearing manufacturers ensure access to high-quality, reliable sealed and unsealed bearings. Rigorous vetting of all raw material suppliers.
- Rigorous Quality Control:
- Incoming Material Inspection: Testing raw materials (metal stock, polymers, chemicals, bearings) against strict specifications.
- In-Process Checks: Dimensional checks, visual inspections, weld integrity testing at multiple stages of production.
- Final Product Testing: Comprehensive testing protocols:
- Load Testing: Destructive and non-destructive testing to verify static and dynamic load ratings (often exceeding industry standards).
- Swivel Torque Testing: Ensuring smooth rotation under load.
- Impact Testing: Assessing durability against shock.
- Rolling Resistance Testing: Measuring effort required to move.
- Environmental Testing: Salt spray testing for corrosion resistance, temperature cycling.
- Brake Effectiveness Testing: Verifying locking force.
- Traceability: Batch tracking for quality assurance and recall management if needed.
- Certifications: Commitment to achieving and maintaining relevant international standards (ISO 9001, etc.) and industry-specific certifications.
- Engineering & Customization Capabilities:
- Dedicated R&D Team: Continuously innovating in materials, designs (like advanced kingpinless systems), and manufacturing processes.
- Application Engineering: Working directly with customers to solve unique mobility challenges.
- Full Customization: Ability to tailor:
- Wheel material, diameter, tread width, hardness, color.
- Fork style, size, material, finish.
- Mounting type and dimensions.
- Bearing type.
- Brake type and configuration.
- Special requirements (ESD, high-temp, chemical resistance, FDA, antimicrobial).
- Global Supply Chain & Logistics:
- Efficient production planning and inventory management.
- Robust logistics partnerships for reliable global shipping to distributors and OEM customers.
- Understanding of international trade regulations and documentation.
Why Choose Goodich? The Brand Advantage
Selecting Goodich as your caster wheel manufacturer means partnering with a company built on core principles that translate directly into value for your business:
- Reliability Engineered In: From material selection to final testing, every Goodich caster is built to perform consistently under its rated load and in its intended environment. Reduced downtime and replacement costs.
- Uncompromising Durability: Investment in high-quality materials (proprietary PU, robust steels) and precision manufacturing ensures casters withstand the rigors of daily industrial use, harsh environments, and demanding cycles, maximizing lifespan.
- Performance You Can Feel: Optimized designs for smooth rolling, easy swiveling (even under load with kingpinless options), and effective braking translate into easier operation, improved ergonomics, and increased productivity.
- Solutions, Not Just Products: Goodich engineers don’t just sell casters; they solve mobility problems. Offering standard ranges and extensive customization ensures you get the right caster for your specific application.
- Global Quality, Competitive Value: Leveraging the efficiency and scale of being a top-tier Chinese caster wheel manufacturer, Goodich delivers world-class engineering and quality at highly competitive prices, offering exceptional ROI.
- Commitment to Innovation: Continuous R&D ensures Goodich stays at the forefront of caster technology, offering access to the latest materials and designs.
- Responsive Support: Technical expertise and customer service focused on building long-term partnerships, providing guidance from selection to after-sales support.
The Global Caster Wheel Market & Goodich’s Position
The global industrial caster wheels market is a dynamic and growing sector, driven by:
- Increasing Industrialization & Automation: Rising demand in manufacturing, warehousing, and logistics globally, especially in Asia-Pacific.
- Growth of eCommerce: Explosion in warehousing and distribution center needs for efficient material handling.
- Healthcare Expansion: Aging populations and advancing medical technology driving demand for medical equipment casters.
- Focus on Ergonomics & Safety: Greater awareness leading to demand for easier-to-move equipment and reliable braking systems.
- Infrastructure Development: Construction booms requiring robust equipment mobility solutions.
- Technological Advancements: Materials science (like advanced PUs), bearing technology, and kingpinless designs improving performance.
As a major Chinese caster wheel manufacturer, Guangdong Goodich Hardware Co., Ltd. is strategically positioned within this growth, particularly in the Asia-Pacific region which is experiencing the fastest expansion. Goodich competes effectively by:
- Offering a blend of high quality and competitive pricing.
- Possessing strong engineering and customization capabilities.
- Maintaining efficient manufacturing and global logistics.
- Continuously innovating to meet evolving market demands (e.g., automation-ready casters, sustainable materials).
- Building strong relationships with global distributors and OEMs.
Maintenance Best Practices for Maximum Caster Life
Investing in quality Goodich casters is step one. Proper maintenance ensures you get the full value and lifespan from that investment:
- Regular Visual Inspections: Check for:
- Visible damage (cracks in wheels/yokes, bent components).
- Excessive wheel wear (flat spots, uneven tread wear, chunking).
- Loose fasteners (kingpins, axle nuts, top plate bolts).
- Proper swivel function (no stiffness or binding).
- Brake engagement and holding power.
- Buildup of debris (string, hair, metal shavings) around axles/swivels.
- Proper Lubrication (Swivel Focus): As detailed in Part 2. Reapply high-quality grease based on environment and usage intensity. Clean old grease/debris first.
- Cleaning: Regularly clean casters, especially in environments with contaminants (dirt, grit, chemicals, food residue). Use appropriate cleaners that won’t damage the wheel material or finish. Pressure wash carefully, avoiding direct high-pressure spray into bearings.
- Avoid Misuse:
- NEVER Exceed Load Rating: This is the single biggest cause of catastrophic failure.
- Match Caster to Environment: Don’t use indoor casters outdoors or standard casters in extreme heat/cold/chemical exposure.
- Avoid Impact & Dropping: Lower equipment gently; avoid hitting curbs or obstacles at speed.
- Use Correctly: Engage brakes properly; don’t drag sideways excessively (puts stress on swivel).
- Timely Replacement: Don’t wait for a caster to fail completely. Replace wheels showing significant wear or damage, and replace entire casters if forks are damaged or swivels become irreparably stiff or loose. Using mismatched or worn casters on the same equipment causes instability and uneven wear.
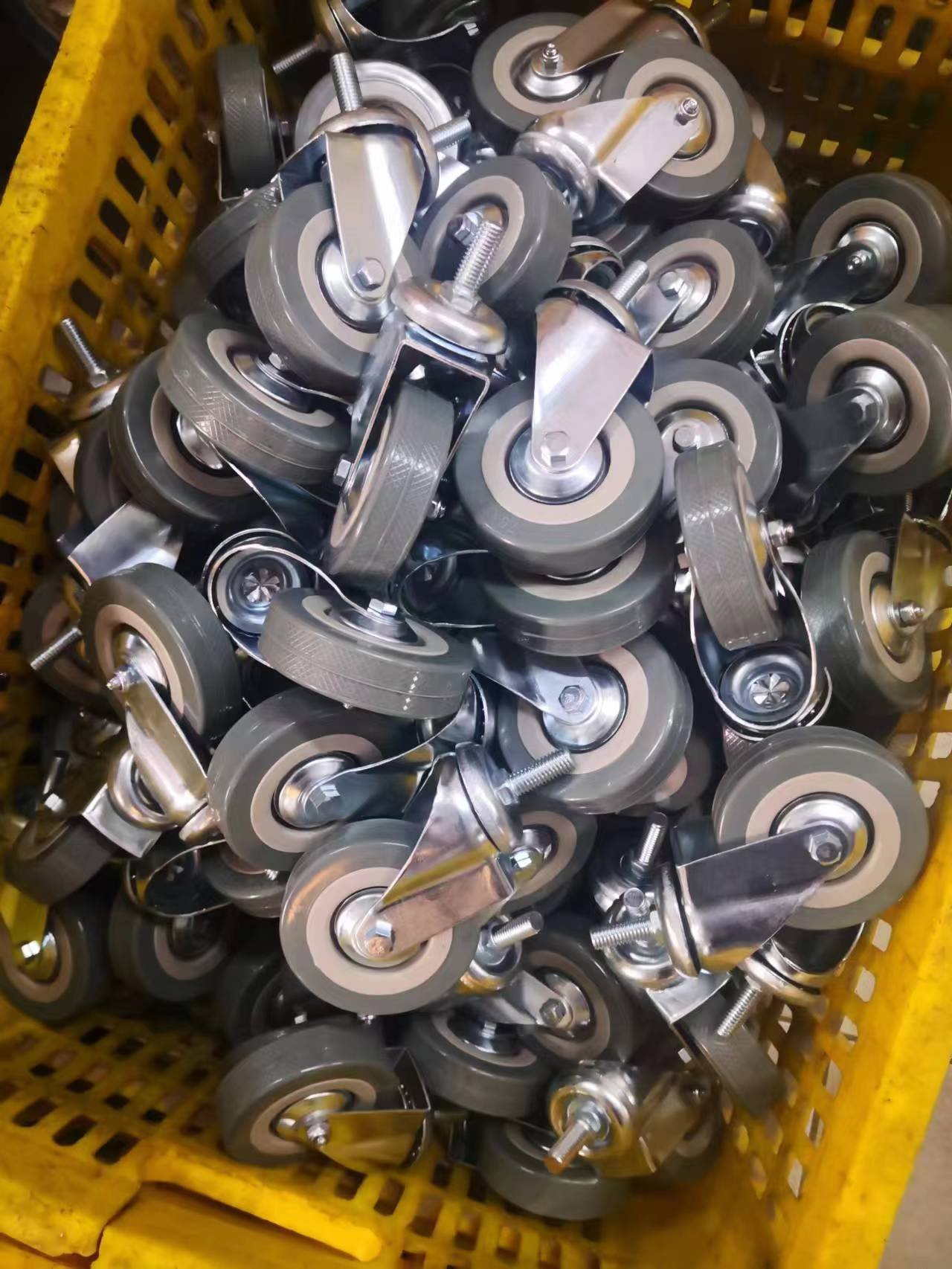
Moving Forward with Goodich
Caster wheels are far more than simple components; they are precision-engineered solutions fundamental to efficiency, safety, and productivity across countless industries. Understanding the nuances of types, materials, bearings, applications, and maintenance is crucial for making informed decisions that impact your bottom line and operational flow.
Guangdong Goodich Hardware Co., Ltd., through its Goodich brand, stands as a testament to the excellence achievable in caster wheel manufacturing. By combining cutting-edge technology, deep materials science expertise, rigorous quality control, and a customer-centric approach focused on providing solutions, Goodich delivers unmatched reliability, durability, and performance. As a leading Chinese caster wheel manufacturer, they offer the global market a powerful combination of world-class engineering and competitive value.
Whether you require robust casters for punishing industrial environments, silent and sanitary solutions for healthcare, corrosion-resistant workhorses for food processing, or aesthetically pleasing mobility for retail, Goodich has the engineering prowess and manufacturing capability to meet and exceed your expectations. Choose Goodich – and experience the difference that truly engineered mobility solutions make. Move with Confidence. Move with Goodich.
Leave a Reply