Imagine a bustling factory floor: heavy machinery humming, production lines flowing, goods swiftly moving from point A to point B. Now, picture everything grinding to a halt because the equipment can’t budge an inch. This is the stark reality without castor wheels industrial – the unsung heroes of mobility. Often overlooked in favour of larger, more glamorous equipment, castor wheels industrial are the fundamental components that transform static machinery into dynamic assets. They are the silent partners in efficiency, reducing worker strain, preventing injuries, minimizing costly downtime, and streamlining operations across countless sectors – from demanding manufacturing plants and sprawling warehouses to critical healthcare facilities.
For over 20 years, Goodich, a leading China castor wheels industrial manufacturer under Guangdong Goodich Hardware Co. Ltd, has engineered robust mobility solutions. We understand that the right castor wheels industrial application isn’t just a convenience; it’s a strategic investment in productivity, safety, and your bottom line. This comprehensive guide dives deep into everything you need to know about industrial casters, empowering you to make informed decisions for your business.
What Exactly Are Industrial Casters?
At its core, an castor wheels industrial is a heavy-duty wheel assembly specifically designed to bear substantial loads and enable the smooth movement of equipment. Think of it as the “mobility package” bolted or mounted onto the base of machinery, carts, racks, and workstations.
- Caster vs. Wheel: It’s crucial to distinguish between the two terms. The “caster” refers to the entire assembly: the wheel itself, the mounting mechanism (like a top plate or stem), the fork that holds the wheel, the swivel mechanism (if applicable), and associated bearings and hardware. The “industrial caster wheel” is specifically the round, rolling component that makes contact with the ground.
- Functionality: Industrial casters support weight and facilitate movement. Swivel casters rotate 360 degrees around a vertical axis, offering exceptional maneuverability for navigating tight corners and crowded spaces. Rigid casters (or fixed casters) only roll in a straight line, providing directional stability, often used in tandem with swivel casters on a piece of equipment. Heavy caster wheels are engineered with reinforced materials and construction to handle extreme weights and withstand punishing industrial environments.
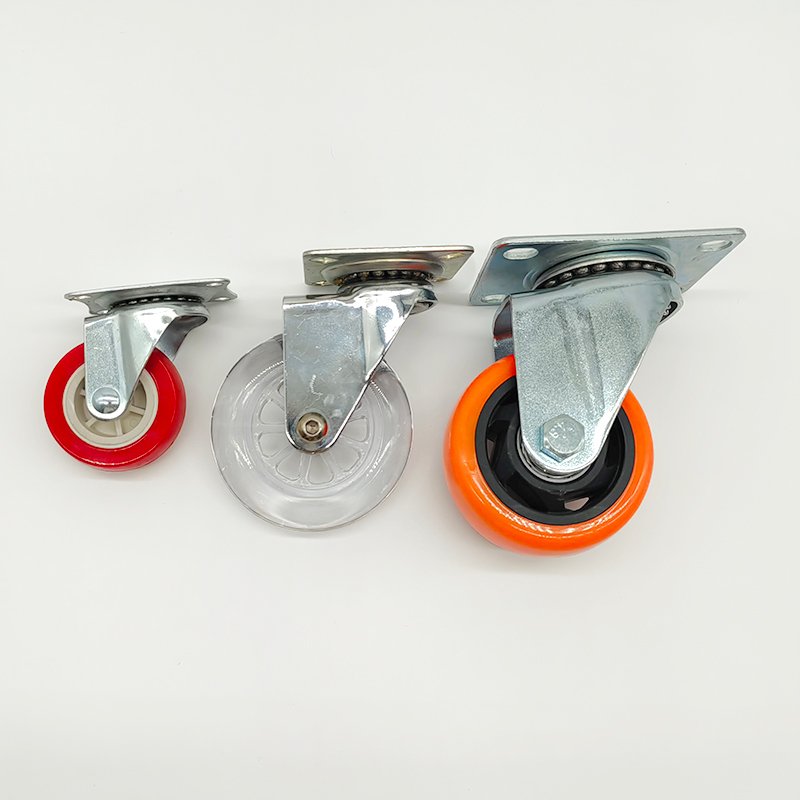
Why castor wheels industrial Are Non-Negotiable for Modern Operations
The importance of high-quality industrial caster wheels transcends mere convenience. They are mission-critical components:
- Enhanced Productivity & Efficiency: Move heavy machinery, loaded carts, or bulky equipment effortlessly. Reposition lines quickly for changeovers. Streamline material flow. This agility directly translates to faster throughput and reduced operational bottlenecks. Downtime spent wrestling with immobile equipment is eliminated.
- Worker Safety & Ergonomics: Manual handling of heavy loads is a primary cause of workplace injuries (strains, sprains, back injuries). Industrial casters drastically reduce the physical force required to move objects, protecting your workforce and lowering injury-related costs and absenteeism.
- Optimized Space Utilization: Easily movable equipment means you can reconfigure floor space as needed for different projects, seasonal demands, or maintenance, maximizing the utility of your valuable square footage.
- Equipment Protection: Smooth-rolling, high-quality castor wheels industrial minimize jarring impacts and vibrations during transport, reducing wear and tear on sensitive machinery and the loads they carry.
- Versatility Across Industries: The applications are vast:
- Manufacturing: Machine bases, assembly carts, tool cabinets, material handling carts.
- Warehousing & Logistics: Pallet trucks, order picking carts, heavy-duty racks, container dollies.
- Healthcare: Hospital beds, medication carts, crash carts, heavy imaging equipment bases.
- Retail: Display units, stock carts, point-of-sale kiosks.
- Aerospace & Automotive: Jigs, fixtures, engine stands, parts carts.
- Food & Beverage: Processing equipment, mixing tanks on mobile bases, sanitation carts.
Demystifying castor wheels industrial Types: Finding the Perfect Fit
Not all industrial casters are created equal. Choosing the right type is paramount for performance and longevity. Here’s a breakdown of the most common configurations offered by leading China caster manufacturers like Goodich:
- Plate Casters:
- Description: Feature a robust, flat steel mounting plate (top plate) for secure attachment, typically using bolts or rivets.
- Strengths: Superior stability and load distribution. Ideal for heavy, continuous-duty applications. Excellent for equipment with ample mounting space underneath. Common in manufacturing, heavy carts, and machinery.
- Goodich Advantage: We offer plate casters in various steel grades (including stainless), thicknesses, and bolt patterns, reinforced for maximum load capacity and durability.
- Stem Casters:
- Description: Utilize a vertical stem (rod) for mounting into a socket or sleeve on the equipment. Two primary subtypes:
- Threaded Stem Casters: Feature a stem with threads (like a large bolt) that screws directly into a tapped hole on the equipment. Provides a very secure, vibration-resistant fit. Popular for furniture, light industrial carts, and medical equipment.
- Grip Ring / Grip Neck Stem Casters: Feature a stem with a retaining ring or flared neck that snaps into a matching socket, allowing quick insertion and removal while preventing pull-out. Common on office chairs, light carts, and service trolleys.
- Strengths: Simpler installation where plate mounting isn’t feasible. Cleaner aesthetic. Goodich provides stems in various lengths, diameters (e.g., 7/16″, 1/2″, 5/8″, 3/4″, 1″), and styles (straight, offset) to suit diverse mounting requirements.
- Description: Utilize a vertical stem (rod) for mounting into a socket or sleeve on the equipment. Two primary subtypes:
- Heavy Duty & Extra Heavy Duty Industrial Casters:
- Description: Engineered for the toughest jobs. Characterized by:
- Massive load ratings (often 1,000 lbs per caster and far beyond).
- Reinforced construction: Thicker top plates, larger diameter stems, forged or heavy-gauge steel forks.
- Kingpinless swivel mechanisms (eliminating a common failure point under shock loads).
- Premium bearings (roller, tapered) for smoother rolling under immense weight.
- Robust wheels designed for high load and floor protection.
- Applications: Foundries, steel service centers, heavy machinery movers, mining equipment, large industrial tanks, shipbuilding. Goodich specializes in engineering these workhorses, often involving custom fabrication to meet extreme demands.
- Description: Engineered for the toughest jobs. Characterized by:
Anatomy of an castor wheels industrial: Understanding the Components
Knowing the parts of a caster helps understand performance and maintenance needs:
- Mounting System (Top Plate or Stem): The interface attaching the caster to the equipment. Dictates mounting method (bolted, screwed, socketed).
- Swivel Section (For Swivel castor wheels industrial):
- Raceway: A channel (often with inner and outer tracks) containing the ball bearings.
- Ball Bearings: Precision balls that reduce friction between the top plate and the swivel base, enabling smooth rotation. Quality bearings are critical for long life and easy swiveling, especially under load. Sealed bearings offer better contamination protection.
- Kingpin / Kingbolt: A central bolt or rivet securing the top plate to the swivel base in traditional designs. Kingpinless designs use precision-machined components for higher strength and reliability under shock loads (common in heavy duty casters).
- Fork (Yoke or Horn): The U-shaped component that holds the wheel assembly. Its design and material thickness directly impact strength and load capacity.
- Wheel Assembly:
- Wheel: The rolling element. Material choice is critical (covered next).
- Axle Bolt & Nut: Secures the wheel within the fork, allowing it to rotate. Must be robust enough to handle the load and rotational forces. Staked or castellated nuts prevent loosening.
- Bearings / Bushings: Reduce friction between the axle and the wheel hub. Options include:
- Plain Bore: Wheel rotates directly on the axle (low cost, low load/speed).
- Bushings (e.g., Oil-Impregnated Bronze, Nylon): Offer better wear resistance than plain bore.
- Roller Bearings: Handle higher loads and speeds more efficiently than bushings.
- Tapered Roller Bearings: Best for highest loads and misalignment tolerance (common in heavy duty).
- Precision Ball Bearings: Excellent for smooth rolling at higher speeds.
- Wheel: The heart of ground contact. Material selection is paramount:
- Cast Iron / Semi-Steel: Extremely hard, high load capacity, excellent wear resistance. Best for very heavy, slow-moving loads on rough surfaces like concrete or steel decking. Can damage soft floors and generate noise. “Semi-Steel” is a high-strength cast iron alloy.
- Phenolic (Thermoset Resin): Very hard, non-marking, chemical and heat resistant, low moisture absorption. Good load capacity. Suitable for high temperatures (e.g., ovens, foundries) and clean rooms. Can be brittle on very uneven surfaces.
- Polyurethane: Excellent all-rounder. High load capacity, superior floor protection (non-marking), good wear resistance, quiet operation, moderate shock absorption, good chemical resistance (varies by compound). Available in a wide range of durometers (hardness, measured on Shore A or D scales – e.g., 85A is common for general industrial use). Goodich offers specialized poly formulations for enhanced oil resistance, static control (ESD), or high-temperature stability.
- Rubber (Solid or Pressed-on): Good shock absorption and vibration dampening, quiet, excellent traction. Protects floors well. Solid rubber offers higher load than pneumatic but less cushioning. Susceptible to oils, chemicals, and extreme temperatures.
- Nylon & Polyolefin (e.g., Polypropylene, HDPE): Hard, lightweight, good chemical resistance, low moisture absorption, non-marking. Good for wet environments and light to medium-duty carts. Can be noisy and transmit vibration.
- Pneumatic (Air-Filled): Excellent cushioning and shock absorption for delicate loads or very rough terrain (grass, gravel). Good traction. Prone to punctures and flats. Require maintenance.
- Flat-Free (Foam-Filled / Solid Elastomer): Offer pneumatic-like cushioning without the risk of flats. Made from solid polyurethane or rubber compounds or foam-filled tires. Ideal where puncture risk is high. Usually heavier and has higher rolling resistance than pneumatic.
- TPR/TPE (Thermoplastic Rubber/Elastomer): A blend offering properties between rubber and plastic – good resilience, floor protection, and often chemical resistance. A versatile option.
- Brakes & Locks: Essential for safety and stability. Types include:
- Total Lock Brakes: Lock both the wheel rotation and the swivel (if applicable). Most secure.
- Wheel Only Brakes: Lock the wheel rotation only; the castor wheels industrial can still swivel.
- Swivel Lock Brakes: Lock the swivel mechanism only; the wheel can still roll straight.
- Directional Lock: Forces a swivel castor wheels industrial to only roll in a straight line.
- Side Brake Lever: Often easier to engage/disengage with your foot. Goodich provides various brake options tailored to application needs and force requirements.
Selecting the Right castor wheels industrial: A Goodich Guide
Choosing the optimal industrial caster wheels requires careful consideration. As a trusted China caster manufacturer, Goodich recommends this step-by-step approach:
- Determine Total Load Capacity:
- Calculate the total weight of the fully loaded equipment (cart + maximum intended load).
- Crucial Rule: Divide the total weight by three (not four) to get the minimum required load capacity per castor wheels industrial. This accounts for uneven floors where one caster might momentarily bear more weight. ALWAYS include a safety margin (e.g., 25-30% over calculated minimum).
- Example: Total Load = 3000 lbs. Min Capacity Per castor wheels industrial = 3000 lbs / 3 = 1000 lbs. Choose casters rated for at least 1300-1500 lbs each.
- Analyze the Operating Environment:
- Floor Surface: Smooth concrete? Rough, pitted concrete? Tile? Grating? Steel decking? Outdoor gravel/grass? Different wheels excel on different surfaces (e.g., soft treads protect smooth floors but wear faster on rough terrain; hard wheels handle debris better).
- Debris: Will casters encounter chips, shavings, cords, or small obstacles? Choose wheels that can roll over debris (e.g., larger diameter, harder tread, specific tread patterns) or consider protective guards.
- Chemicals/Oils: Are spills or exposure to solvents, oils, acids, or caustics likely? Select chemically resistant wheel materials (e.g., Polyurethane, Nylon, Phenolic) and corrosion-resistant hardware (e.g., Zinc plating, Stainless Steel).
- Temperature Extremes: Very high heat (ovens, foundries) or freezing cold? Standard materials may fail. Specify high-temp wheels (e.g., Phenolic, specialized high-temp Polyurethane) or cold-rated materials.
- Cleanliness Requirements: Food processing, pharmaceuticals, electronics manufacturing? Require non-marking, easy-to-clean, corrosion-resistant castor wheels industrial (e.g., Stainless Steel frames, Polyurethane or Phenolic wheels). ESD (Electrostatic Discharge) wheels may also be needed.
- Outdoor Use: Requires UV-resistant wheels and corrosion-resistant frames/mountings (Stainless Steel or hot-dip galvanized). Pneumatic or flat-free tires often preferred for uneven ground.
- Define Mobility Needs:
- Maneuverability: Does the equipment need to turn corners easily? Use a combination of swivel and rigid castor wheels industrial (e.g., 2 swivel, 2 rigid is common). All-swivel offers maximum maneuverability but can be harder to steer straight. All-rigid is only for straight-line travel.
- Precision Placement: Is precise positioning critical? Brakes with swivel locks are essential.
- Speed: Will equipment be towed or pushed at higher speeds? Require high-quality bearings (roller or precision ball) and potentially larger diameter wheels for stability.
- Choose Mounting Style:
- Plate Mount: Best for heavy loads, maximum stability, and permanent/semi-permanent attachment. Requires accessible flat surface.
- Stem Mount: Ideal where plate mounting isn’t possible or for lighter applications. Threaded stem for secure attachment; grip ring for easy removal. Specify stem type and size carefully.
- Select Wheel Material & Size:
- Refer to the wheel material guide above and match material properties to your environment (floor type, debris, chemicals, noise, load).
- Diameter: Larger wheels roll more easily over obstacles and cracks, require less effort to start rolling, and often have higher load capacities. Consider under-clearance constraints.
- Tread Width: Wider treads distribute weight better on soft surfaces (like asphalt or turf) and offer more lateral stability. Narrower treads may be needed for tight spaces or tracks.
- Consider Special Requirements:
- Track Systems: Require flanged wheels (single or double flange).
- Non-Magnetic Environments (e.g., MRI): Require non-magnetic materials throughout (e.g., specific grades of Stainless Steel like 316, Aluminum, Polyurethane, Phenolic). Note: Common Stainless Steel (like 304) is often magnetic!
- ESD/Electric Conductivity: Require wheels specifically designed to dissipate static electricity or provide electrical grounding.
- High Sanitation: Require fully welded, crevice-free designs (e.g., Stainless Steel) for easy cleaning.
- Extreme Loads or Conditions: Often necessitates custom engineering. This is where Goodich excels.
Maintaining Your castor wheels industrial
Like any vital component, castor wheels industrial perform best and last longest with proper care. Goodich recommends this maintenance regimen:
- Regular Cleaning: Dirt, grit, and debris are the enemy of bearings and swivel mechanisms. Wipe down wheels and forks regularly. For heavy buildup, use a brush and mild detergent (avoid harsh chemicals that could damage wheels or seals). Rinse thoroughly if washed.
- Visual Inspections: Schedule frequent checks for:
- Wheel Wear: Flat spots, cracking, chunking, excessive tread wear, or distortion. Worn wheels increase rolling resistance and can damage floors.
- Fork Damage: Cracks, bends, or distortion. Critical for safety.
- Mounting Integrity: Loose bolts, rivets, or stems? Tighten immediately! Loose stem grip rings? Replace if worn.
- Swivel Function: Does the castor wheels industrial swivel freely without binding or excessive play? Binding indicates contamination or lack of lubrication; excessive play suggests wear.
- Brake Function: Do all brakes engage and disengage positively and hold securely?
- Lubrication (Where Applicable): Some swivel mechanisms (especially older kingpin types) and certain axle bearings benefit from periodic lubrication. Consult the manufacturer’s specs (Goodich provides this). Use the recommended lubricant sparingly – excess attracts dirt. Note: Many modern sealed bearings and kingpinless casters are “lubed for life.”
- Tightening Hardware: Periodically check and tighten axle nuts and mounting hardware (bolts, nuts) to manufacturer specifications. Vibration can loosen them over time.
- Timely Replacement: Don’t wait for catastrophic failure. Replace worn wheels, damaged forks, or malfunctioning brakes promptly. Using damaged casters is a safety hazard and can damage equipment or floors. Goodich stocks a vast range of replacement wheels and components.
1.5 Inch rubber Plated Swivel Industrial Castors
4/5/6/8 Inch Rubber Industrial Castor Wheels
5 caster wheels
caster and wheel
Caster Factory 2/3/4 Inch Pu Material Industrial Castors And Wheels
caster wheel
caster wheels 3 inch
caster wheels 4 inch
casters with brakes
Customized Durable PVC PP Industrial Caster Wheel For Trolley
Furniture Caster 2/3/4 Inch Castor Wheels Industrial Without Lock
heavy duty castor wheels
industrial casters wheel
Industrial casters wheels heavy duty
Locking caster wheels
Troubleshooting Common Industrial Caster Problems
Even well-maintained castor wheels industrial can encounter issues. Here’s how to diagnose and fix common problems:
- Caster Wobble / Shimmy: Uncontrolled side-to-side oscillation, especially at speed.
- Causes: Loose mounting hardware, worn kingpin (if applicable), worn or damaged swivel bearings, uneven wheel wear, bent fork.
- Fix: Tighten all mounting bolts/stem nuts. Inspect swivel mechanism for wear; replace worn bearings or the entire swivel section if necessary. Replace unevenly worn wheels. Check forks for straightness; replace if bent.
- Excessive Swivel Resistance (Binding): Hard to turn the caster.
- Causes: Dirt/debris in swivel raceway, damaged or dry bearings, bent kingpin or fork, overtightened swivel mechanism.
- Fix: Clean thoroughly. Lubricate if specified and accessible. Inspect for damage; replace damaged components. Ensure swivel isn’t overtightened.
- Hard Rolling / Excessive Effort Required:
- Causes: Wrong wheel type for floor/load (too soft, too small diameter), worn wheel bearings (seized or dry), low tire pressure (pneumatic), wheel deformation (flat spots), brake dragging, debris jammed in fork/wheel.
- Fix: Verify wheel suitability (material, size). Lubricate or replace wheel bearings. Inflate pneumatic tires. Replace deformed wheels. Disengage/release brakes fully. Remove debris.
- Uneven Wheel Wear:
- Causes: Equipment overloaded (exceeding caster capacity), uneven weight distribution on the equipment, misaligned castor wheels industrial (e.g., rigid casters not pointing straight), dragging brakes, abrasive floors.
- Fix: Ensure load is within capacity and evenly distributed. Check alignment of rigid casters. Ensure brakes fully disengage. Consider harder or more wear-resistant wheels if abrasion is the primary cause.
- Noisy Operation (Squeaking, Grinding):
- Causes: Lack of lubrication in swivel or bearings, dry wheel bore on axle, worn bearings, damaged wheels, debris caught in mechanism.
- Fix: Lubricate if applicable. Clean thoroughly. Replace worn bearings or damaged wheels.
- Brake Failure (Won’t Hold or Won’t Release):
- Causes: Worn brake pad/shoe, damaged brake mechanism, debris under brake pad, loose mounting.
- Fix: Inspect brake components; replace worn parts. Clean debris. Tighten mounting hardware. Ensure linkage isn’t bent or obstructed.

Beyond Standard: Goodich – Your Partner in Industrial Mobility
As a premier China castor wheels industrial manufacturer, Guangdong Goodich Hardware Co. Ltd stands apart. We don’t just sell casters; we engineer mobility solutions. Here’s why global industries trust Goodich:
- Engineered for Extreme: We specialize in heavy duty castor wheels industrial and extra heavy duty casters, pushing the boundaries of load capacity (up to [Specify High Load Capacity, e.g., 30,000 lbs per caster+] and durability for mining, steel, foundries, and heavy machinery.
- Material Mastery: Deep expertise in metallurgy and polymer science allows us to select and formulate the optimal materials – from high-strength forged steel and specialized stainless alloys to advanced polyurethane compounds offering unparalleled wear, chemical, and temperature resistance.
- Kingpinless Innovation: Our heavy-duty swivel casters often feature rugged kingpinless designs for maximum reliability under shock loads and continuous stress.
- Precision Bearings: We utilize premium roller bearings, tapered bearings, and precision ball bearings tailored to load and speed requirements, ensuring smooth rolling and long service life.
- Custom Fabrication Powerhouse: Standard solutions not cutting it? Goodich excels in castor wheels industrial. Our engineering and manufacturing teams collaborate to design and build solutions for unique applications – from specialized mining wheels to intricate stem adapters for legacy equipment. We handle complex geometries, extreme dimensions, and specific material mandates.
- Rigorous Quality Control: Every Goodich castor wheels industrial, from standard to custom, undergoes stringent quality checks. We adhere to international standards (mention specific ones if applicable, e.g., ISO 9001) to guarantee performance, safety, and longevity.
- Global Support & Logistics: Based in China with a global outlook, we offer efficient logistics and responsive technical support to partners worldwide.
Conclusion: Invest in Mobility, Invest in Efficiency with Goodich
castor wheels industrial are far more than simple wheels; they are the linchpins of operational fluidity, safety, and productivity. Choosing the right castor wheels industrial application – considering load, environment, mobility needs, and durability – is a critical decision impacting your bottom line and workplace well-being.
Don’t leave your mobility to chance or compromise with subpar components. Partner with Goodich, a China caster manufacturer dedicated to engineering excellence and robust solutions. Whether you need reliable standard castor wheels industrial, rugged heavy duty industrial casters, or a completely custom engineered solution, we have the expertise and manufacturing prowess to deliver.
Ready to transform your equipment’s mobility? Contact Goodich today!
- Explore our extensive range of high-performance industrial casters.
- Request expert consultation to select the perfect casters for your specific application.
- Discuss your custom caster needs with our engineering team.
- Experience the Goodich difference in quality, durability, and value.
Visit our website or contact our sales team now to discover how Goodich can keep your world moving forward.
About Guangdong Goodich Hardware Co. Ltd:
Guangdong Goodich Hardware Co. Ltd is a leading innovator and manufacturer of premium castor wheels industrial and wheels. Based in China, we serve global industries with a commitment to engineering robust, reliable, and efficient mobility solutions. Our focus on quality materials, advanced manufacturing, and custom capabilities makes Goodich the trusted partner for businesses demanding the best in industrial movement. From standard plate casters and stem casters to massive mining wheels and specialized stainless steel designs, Goodich delivers performance you can roll with.
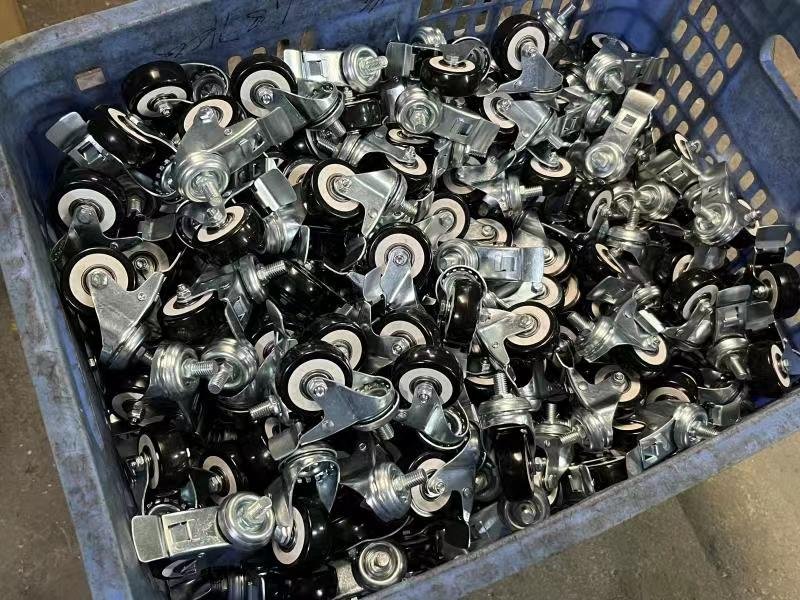
Leave a Reply