The term “caster” is well-known and widely used, yet many people often confuse it with “wheel.” As industries have evolved, the demand for casters has grown, leading to the development of a specialized caster industry. This guide aims to help you understand the various aspects of wheels and castors
What Is a Caster?
A caster is a combination of a bracket and a wheel, designed to be installed under various types of equipment and machinery. This allows for easier movement and significant labor savings. Casters can be made from different materials, such as stainless steel brackets paired with nylon wheels or other materials like polypropylene (PP), depending on the application, load requirements, or installation height.
Caster Wheel Sizes
Caster wheels come in various sizes, which can generally be categorized into four groups based on their load capacity:
- Light Wheels: Ranging from 1 to 3 inches in diameter (25mm to 75mm), these wheels typically support loads between 10 and 150 kg.
- Medium Wheels: With diameters from 3 to 5 inches (75mm to 125mm), these wheels can handle loads from 100 to 210 kg.
- Heavy-Duty Wheels: Measuring 6 to 12 inches in diameter (150mm to 300mm), these are capable of supporting loads from 600 kg up to 1 ton.
- Special Dimensions: Custom casters can be made to specific requirements, including unique wheel diameters, widths, or materials.

Common Caster Materials
The choice of material significantly affects the caster’s performance and durability:
- Polypropylene (PP): Known for its toughness and excellent chemical resistance, PP is a cost-effective alternative to nylon, although it can become brittle over time.
- Thermoplastic Rubber (TPR): Ideal for environments like hospitals due to its silent operation and wear resistance, TPR is not suitable for high-temperature situations.
- Polyurethane (PU): This environmentally friendly material is visually appealing and smooth but lacks wear resistance and can break easily.
- Rubber: With excellent insulation and high elasticity, rubber casters can withstand high temperatures but may leave marks on floors over time.

Manufacturing Process of Caster Wheels
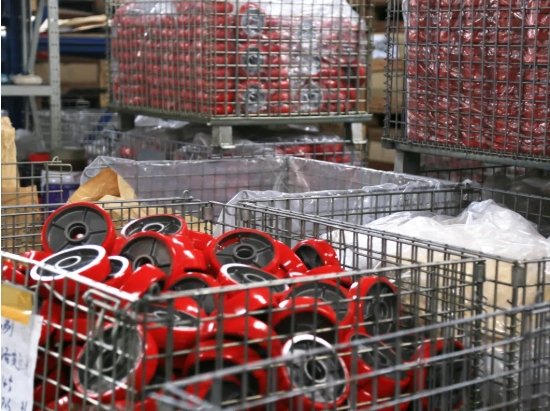
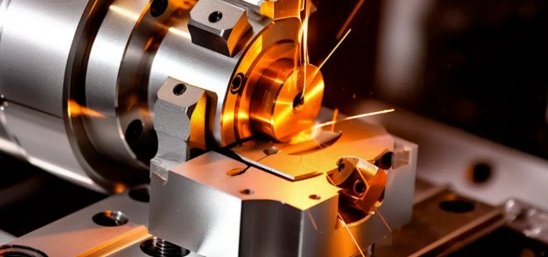

Material Selection
Choosing the right material is crucial and should be based on the intended application and environmental conditions.
Molding
For rubber or plastic wheels, the process begins with heat treatment, followed by injection molding to shape the caster. After shaping, the wheels undergo cooling and curing before being inspected for defects.
Metal Components
For metal wheels, the manufacturing process typically involves cutting, punching, welding, and shaping without the need for heat treatment.
Assembly
Once the caster components are complete, they are assembled with bearings, screws, and other accessories to create a fully functional product. Automation has streamlined this process, enhancing efficiency and ensuring quality.
Finishing and Coating
Casters undergo surface treatments like galvanizing or chromium plating to prevent corrosion and extend lifespan. Electrophoresis black treatment offers an environmentally friendly option for coating.
Quality Control
Quality control is essential to identify potential defects and ensure that each caster meets established standards.
Packaging and Distribution
After quality checks, casters are packaged for delivery. Post-sales support is also available for any issues that may arise during use.
Types of wheels and castors
Casters are ubiquitous across various industries, each with specific requirements. They can be categorized by load capacity and application:
- Load Categories:
- Light Duty Casters
- Medium Duty Casters
- Heavy Duty Casters
- Super Heavy Duty Casters
- Industry Applications:
- Industrial Casters
- Furniture Casters
- Medical Casters
Each type is designed to enhance work efficiency and provide stability and ease of movement for different equipment and furniture.
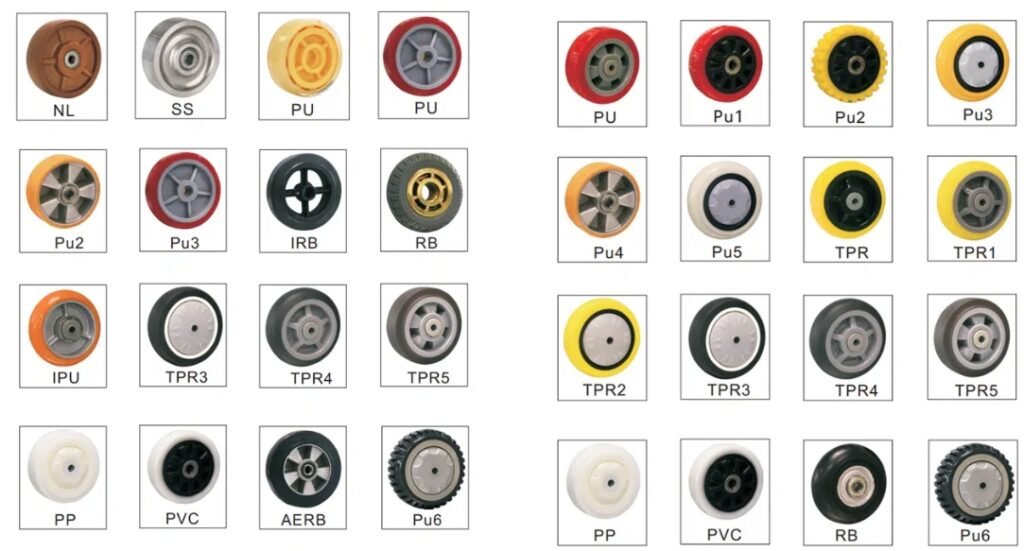
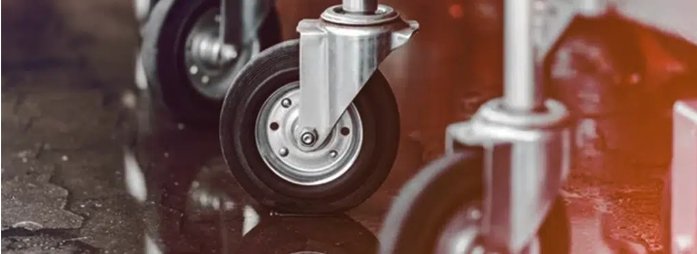
How to Remove Caster Wheels
- Tool Preparation: Gather necessary tools.
- Clear the Area: Ensure the workspace is free of obstacles.
- Lock the Equipment: Secure the equipment to prevent movement.
- Examine the Attachment: Identify how the caster is attached.
- Inspect and Clean: Check for dirt or debris and clean if necessary.
- Lubricate (Optional): Add lubricant if needed.
- Replace or Reinstall: Follow instructions if replacing.
- Dispose or Store: Properly store or dispose of old casters.
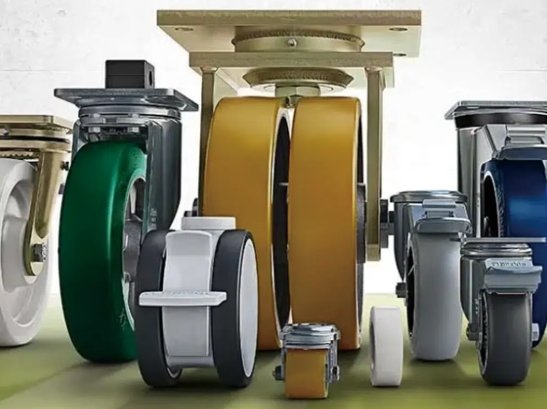
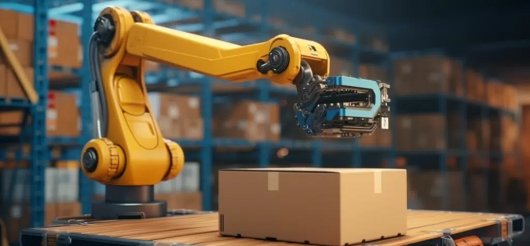
How to Choose the Right Caster Wheel
Selecting the appropriate caster is crucial for efficiency and safety. Consider the following factors:
- Load Capacity: Ensure the caster can support the weight of the equipment.
- Wheel Diameter: Larger wheels offer greater stability and load-bearing capacity, while smaller wheels may fit confined spaces.
- Material: Choose materials based on the application—metal for heavy loads, plastic or rubber for lighter, quieter use.
- Swivel vs. Rigid: Decide between swivel casters, which allow flexible movement, or rigid casters, which provide fixed positioning.
Routine Maintenance for Caster Wheels
Regular maintenance is vital for extending the life of casters and ensuring optimal performance. Here are key maintenance tasks:
- Check the Wheels: Inspect for cracks or wear and clean regularly without harsh chemicals.
- Lubrication: Apply lubricant to bearings as needed, but avoid over-lubrication.
- Inspect Fasteners: Regularly tighten screws and nuts to prevent loosening.
- Avoid Impact and Overload: Prevent damage by avoiding impacts and adhering to load limits.
- Check the Axle: Ensure the axle is secure and not bent.
By following these maintenance practices, you can enhance the performance and longevity of your casters, ensuring stability and safety for your equipment.
Leave a Reply